The Ciseal Blog
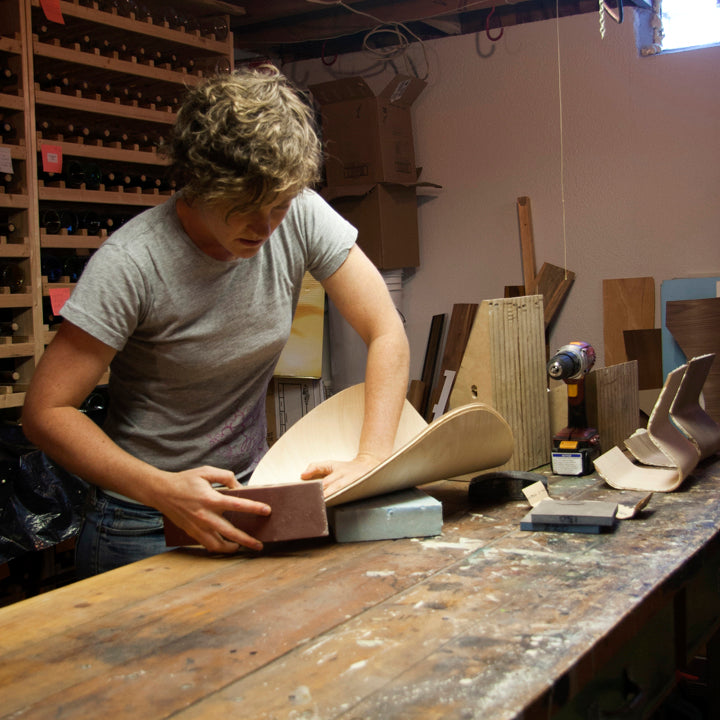
Is “Handmade” Just a Marketing Gimmick?
Interest in handmade products is on the rise - and for good reason. The shift towards purchasing handmade products is a counterpoint to the impersonal mass production and mindless purchasing we’ve become accustomed to in the past 60 years. For many who are weary of the impact that large corporations have had, buying handmade is the socially, economically, and environmentally responsible thing to do. But in this day and age of accessible technology, many consumers are not sure they can trust the “handmade” label. Handmade is a big marketing angle in our industry, and we wanted to take a second to discuss where we stand.
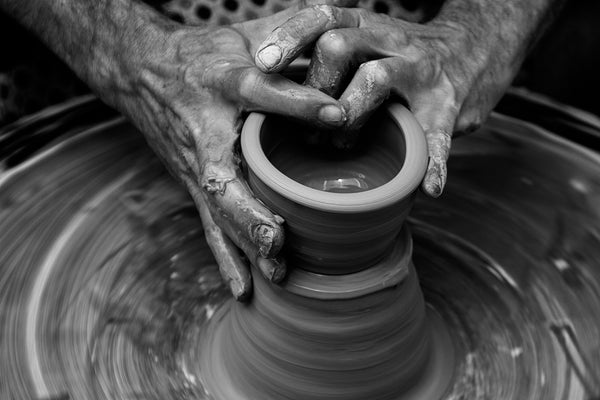
When you can find thousands of identical “handmade” pieces of furniture at big box stores it’s easy to give a cynical side eye at the mention of “handmade.” As soon as a product is labeled “handmade,” a massive gray area emerges in your mind. From doing everything exclusively by hand with hand-foraged materials and handmade tools to hand-finishing a bowl that was carved on a computer-guided lathe - there are many interpretations along the spectrum and it’s easy to see why “handmade” can be so confusing. It comes down to deciding for yourself where along the spectrum you’re most comfortable.
To discover where you stand, please feel free to ask questions like, whose hands made it, where it was made, out of what materials, with what methods, and was the maker respectfully compensated? Any maker of handmade products should be happy to answer all of these questions and more, and if they’re not, then that’s probably a good sign to move on. With your questions answered, you will be able to make more informed decisions that leave you feeling satisfied and proud of your purchase.
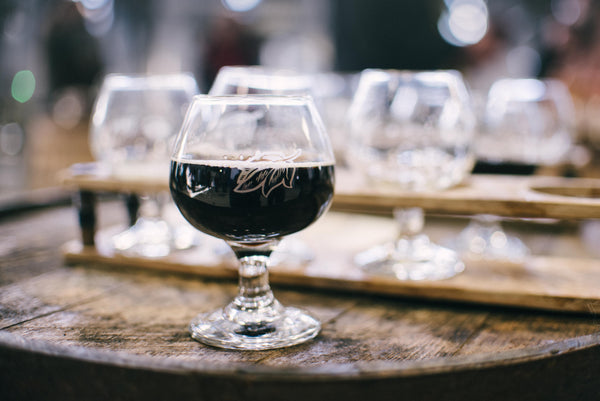
Photo by Alice Donovan Rouse on Unsplash
For me, I find it helpful to think of handmade as craft made, and when I think of craft made, I’m reminded of craft beer - all of those tiny breweries that have emerged in the past few years who produce delicious, flavorful, and unique beers. Craft breweries create their brews with passion and love, and that’s plain to taste in their mouth-watering products. They may not all be focused on creating their beer completely by hand like in centuries past because of volume demands or health and safety factors, but their craft remains their focus. It’s a responsibility to the ingredients, the process, the final product, and the customer - not just the executives and the shareholders - that set craft breweries apart from their larger corporate counterparts. That essence is what I look for in “handmade” products for my home. I want to know that the materials are sustainably and responsibly sourced, the methods used to make it will last, the design is something I won’t tire of, and the maker is adequately compensated so that they will be able to continue to make their lovely wares for years to come.
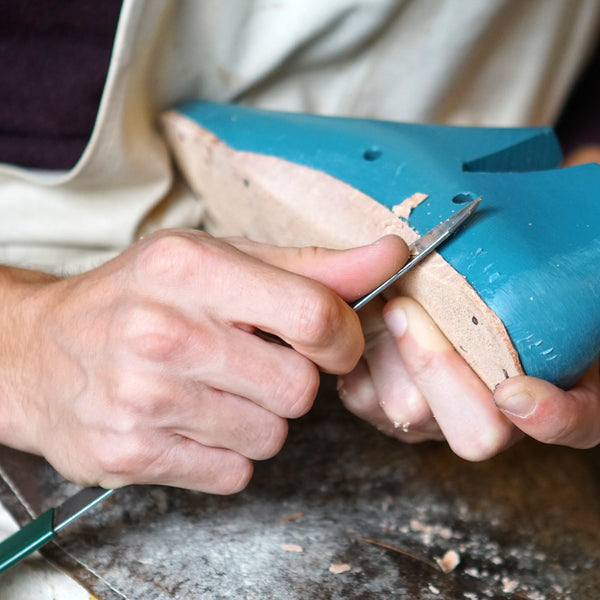
Photo by Raoul Ortega on Unsplash
Ciseal’s interpretation of handmade allows for the use of machinery and technology where it makes sense in improving the quality of the final product. We don’t hand-forage or reclaim wood from old barns because our craft doesn’t really work well with those methods. The veneers we use are sustainably sourced, and they are produced on computer-guided saws that maximize the use of the natural material. We hand-cut each layer of veneer to shape, then the glue is brushed on by hand. Our products are pressed to shape by using either manual clamps or a motorized vacuum press depending on the design’s requirements. We use hand-operated power tools like saws, sanders, and drills to prepare our products for their final hand-sanding. Then we apply a hand-rubbed finish to preserve and protect each piece. By the time it makes its way to you, each piece has had our hands all over it. Eventually, we will probably consider using industrial presses with machined dies to bend our plywood when our volume necessitates it, but much of our process will always remain very hands-on.
As a small business, it’s a challenge to balance design, production, and value to our customers all while making sure the business is producing a healthy profit that will ensure that it stays around. Someday, that balance may lead us to consider producing our products with a mass-manufacturing approach, and when that time comes we will weigh all of the costs and benefits. For now, we will stick to our almost completely hands-on process because we love what we do and how we do it and we believe it makes our products better for it. Thank you to everyone around the world who find value in our work the way it is, and thank you to those of you who want to see us grow into the biggest bent plywood manufacturer in the world. We’re humbled by your support.
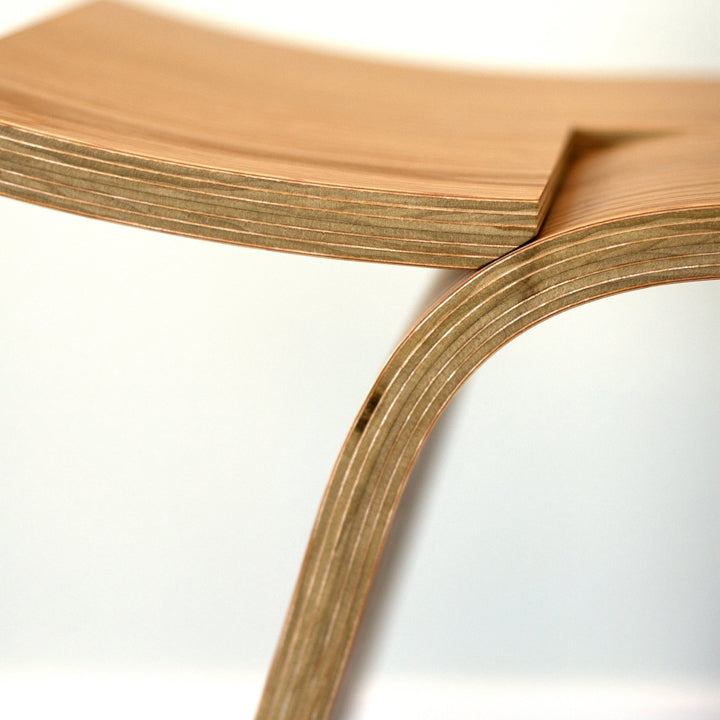
How It's Made: Plywood
If you haven’t noticed, plywood is kind of our favorite material. One reason we love it is for it’s efficient use of the trees it is made out of. Between hardwood and plywood, plywood is by far the more sustainable option because It’s the most efficient use of the tree. Plywood utilizes the entire tree trunk with no off cuts and very, very little waste. You can’t get much more efficient! If you’re curious about how plywood is made, check out some of our favorite process videos below:
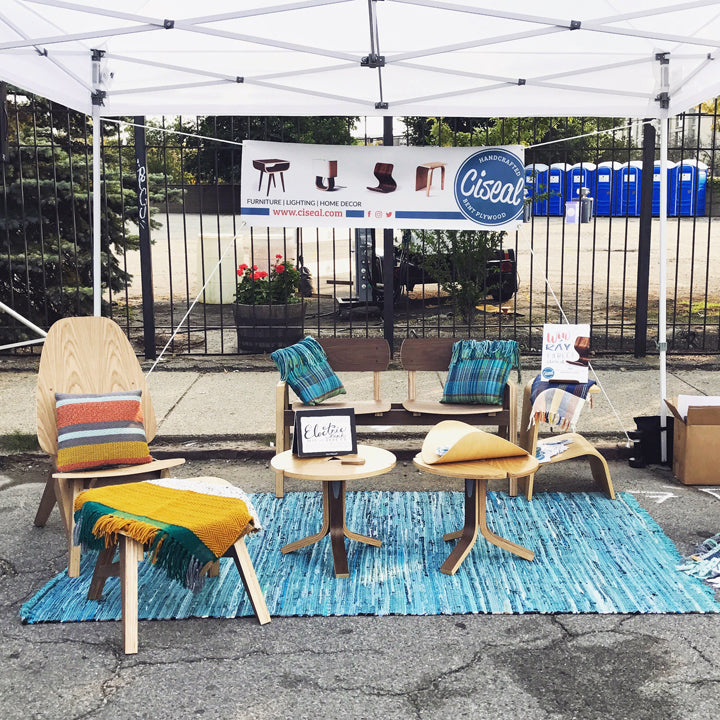
2017 Renegade Craft Fair Detroit Recap
We had an absolutely lovely time at this past weekend’s Renegade Craft Fair at Detroit’s Eastern Market. It was a rare sunny and hot September weekend in Detroit, and the crowds were happy to soak up the sun while perusing the handmade goods. From the unique, handmade vendors to the delicious food trucks and the super amazing DJ, the fair was a wonderful time!
The feedback we got on our brand new furniture was great! I had just finished the bench, lounge chair, ottoman, and cocktail tables the night before, so I was excited to see what everyone thought of them. It was an overwhelming positive response! People would consistently catch a glance of our booth and be drawn by their delighted eyes directly over for a better look. The comments of “absolutely gorgeous,” “so unique,” and “I’ve never seen anything like it” were music to my ears all weekend. I may make a few tweaks to the new designs, but they will be in the shop soon. Be sure to sign up for our email newsletter to be the first to know when they’re released.

Photo: Renegade Craft Fair
Our display of furniture was brought to life by Electric Pink Crafts’ bright and beautiful pillows, blankets, and rugs. Thank you so much, Julia, for creating some gorgeous textiles and letting us borrow them for the fair! Be sure to check out Julia’s shop - her textile designs are perfect complements to our furniture.
It was a wonderful fair overall. I loved meeting some of our Instagram fans and talking with people who learned of us for the first time at the fair. Thank you to everyone who came out! And a big thank you Dan & Jen for all of your help preparing for the fair and helping to man the booth!

How the Eames Bent Plywood LCW is Made
Howdy, bent plywood fans! I came across this video the other day and just had to share it with you. It’s all about how the Eames Lounge Chair Wood (LCW) came to be. They go back to the beginning and share how plywood - normally a construction material - became a modern furniture material through the creative eyes of Charles & Ray Eames. Then, the video goes behind the scenes and shows the actual process used to make the chairs today. It all happens just on the other side of our lovely state in Grand Rapids, Michigan. Watching it left me drooling and excited to make some bent plywood things myself, so enjoy!
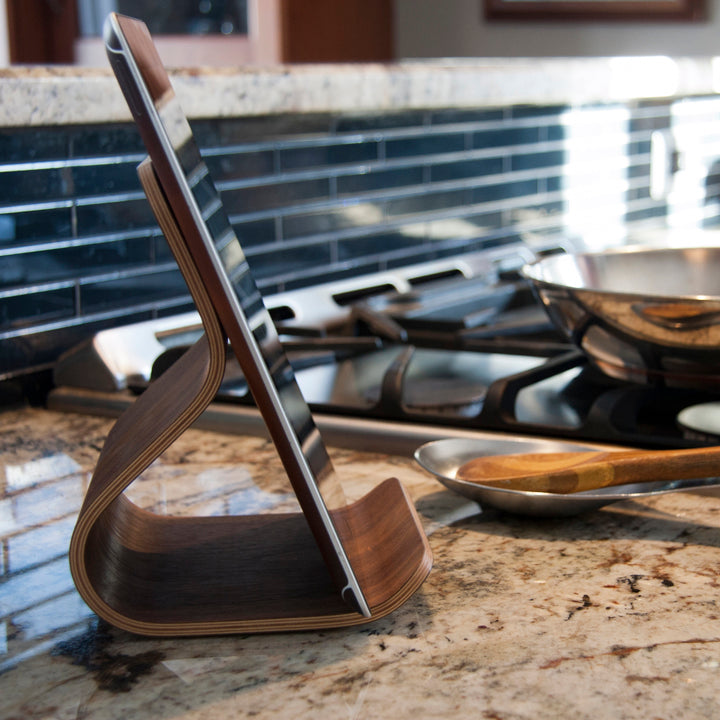
The Story Behind the Ray iPad Stand
I often get asked about how a Ciseal product comes to be - what inspires the designs, what the process involves, how the products are made, etc. Each Ciseal product has a different story behind it and a different inspiration. Some products were created to solve a problem or to fill a need. Others were inspired by a shape or place or thing and I set out to reinterpret that inspiration as a bent plywood object. With such different inspirations, each one of Ciseal's products is unique in and of itself, so the process of making them varies a bit as well. That variation is what’s so magical to me, and it's why I find so much joy in making each one. To kick off this behind the scenes series, lets start with Ciseal’s first product - the Ray iPad Stand.

Photo: Cablik Enterprises
In setting out to design and make the Ray, I gave myself a design brief: Create a Mid Century modern inspired tablet stand. Mid Century was important to me because I love the style's combination of simple, modern lines with natural elements such as wood. Also, I’m a bit obsessed with bent plywood (if you haven’t noticed by now), and Mid Century design is where bent plywood first found it’s form. And it was to be a tablet stand because I wanted to create a product that would be useful as well as beautiful, and the tablet stands I had seen up until then just didn’t cut it from an aesthetic perspective. Sure, they functioned well by holding a tablet upright, but most of them were anything but beautiful.

Photo: Hive Modern
The design process began with a focused sketching session of just getting as many different ideas onto paper as possible. I printed out a few mid century inspired interior photos for inspiration and went to work on a fury of thumbnail sketches with pen and paper. Ultimately, the one tiny sketch I felt most drawn to was one inspired by the Eames LCW chair that was sitting in the corner of one of the living room photos I used for inspiration. That perfectly molded piece that connects the seat to the back had just the right combination of beauty and usefulness that I was looking for in my iPad stand design.
Having chosen a design direction, I had to refine it into a shape that would work perfectly for the purpose of holding an iPad while at the same time retaining the clean, modern shape of it’s inspiration. This is where my engineering side gets to wield it’s numbers and calculations while the design side babysits and advocates for something that’s really, really good looking. The more versatile the design the better, so I wanted it to be able to hold as many different sizes of tablets, books, photos, etc. as possible. I won’t bore you with the details, but the final design you see is the result of many, many sketches, mock ups, and calculations. I played with so many angles and depths and widths to find the perfect viewing angle and the most versatile dimensions.
With the design finalized, it was time to make the real thing! I made a two part mold for this one to ensure there would be even pressure across the entire surface.
Once the glue has dried, I take it out of the mold. The edges are then cut off to even out the layers and trim the stand to size.
And then the edges get sanded and sanded and sanded to polish up the lovely layers. Seriously, sanding takes soooooo much time, but it’s absolutely worth it in the end!
Then we hand wipe the polyurethane finish onto the stand in multiple coats with even more sanding in between each one to create a super durable finish. Then cork feet are added to keep it from sliding around and our stamp of approval is added once everything is perfect.
With the stand complete, it came time to decide on a name for it. Being influenced by Charles & Ray Eames' LCW chair, I thought that naming it after Ray Eames would be more than appropriate. Ray's influence as a woman designer in the Mad Men era is such an inspiration to me, so the name has a double significance. The Ray iPad Stand is available in our three standard woods: Birch, Oak, and Walnut along with a Ray exclusive wood, Sapele. Check them out in our shop and get one for your iPad!
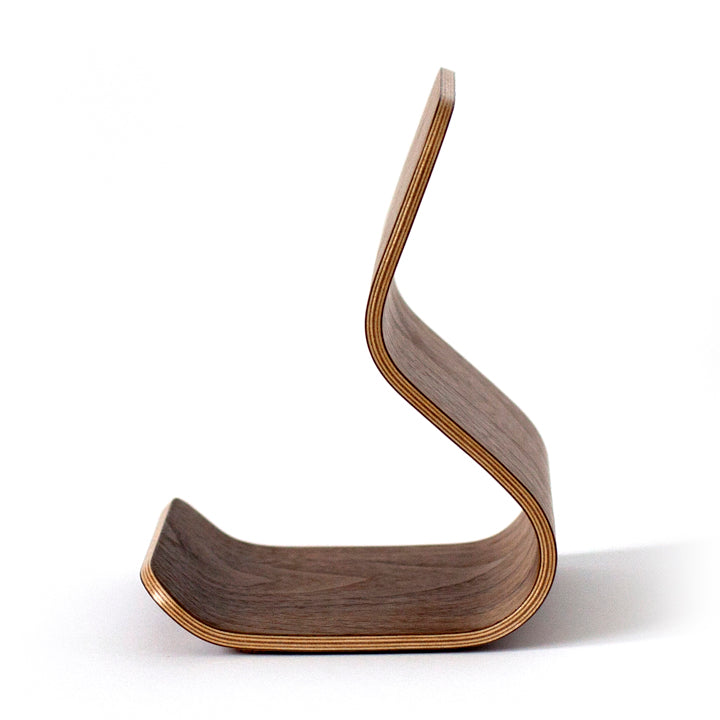
Why Bent Plywood?
I get asked all the time how I got started in hand crafting bent plywood furniture and what's my inspiration, so here's some of the story:
Born and raised in the suburbs just north of Detroit, there wasn't a big emphasis on art or design. They were subjects I enjoyed in school, but I felt a huge push towards pursuing a career in math or science. Therefore, engineering was my first pursuit.
Fortunately, through my job at the GM Technical Center in Warren, MI, I was introduced to the simple, understated beauty of mid century modern architecture and design. I was always the one who volunteered to represent engineering in meetings at the design center - not only did I get to experience the beautiful design center lobby with its gorgeous suspended stairs that lead up to the studios, but it was my chance to pick designers brains on how they got to where they are. I have since come to learn about the history and intent of the campus’ design and it is definitely the spark that led me in the direction of becoming a designer (Dwell magazine has a great little article on the design of the GM Technical Center here).
While at GM I enrolled at The College for Creative Studies in Detroit, and it only took about one semester of juggling work and school for me to realize that pursuing design full time was my next step. With the freedom to focus just on school, I was able to explore classes beyond my product design major. My junior year I took a furniture class that focused on bent plywood, and I was hooked. I loved the process of designing and hand making durable, functional products from what was previously flimsy, bendy wood.
After graduating from CCS, I started making the Ray tablet stand and other bent plywood things in my spare time. It eventually grew from a fun hobby making dust in my parents cluttered basement to a legitimate business with happy paying customers.
Modern classics of the Mid-Century and Danish Modern designers like Charles & Ray Eames, Eero Saarinen, Florence Knoll, Harry Bertoia, Arne Jacobson, and George Nelson are the biggest influences of my designs. They inspire me with their nods toward nature, respect for materials and clean, unadorned designs that are both functional and beautiful.
For each piece I make, I build a form by hand, cut out individual layers of material, then carefully apply glue to each layer, clamp the layers to the form, trim, sand and rub on the finish. Each piece takes days to complete. It’s definitely faster and cheaper for huge manufacturers to mass-produce molded plywood products on robotic assembly lines half a world away, but their products lack a certain soul. There’s an attention to detail, a love of material, a passion for perfection that is evident in a handmade Ciseal product. My furniture and accessories are designed to be used, loved, and enjoyed every day - hopefully for years to come. Nothing is more beautiful than a bent plywood piece that shows through its nicks, scratches, and worn veneer that it's been loved for a lifetime.
Check out what's resulted from this journey: Ciseal's Collection
If you'd like to follow along on the rest of this adventure, feel free to sign up for our email newsletter